工場内に山積みされている長い棒状のものが、「X PROTOTYPEアイアン」の素材である軟鉄S20Cです。日本の企業が製造しているもので、株式会社ササキの佐々木政浩社長によると、海外製とは「大きな違いが出る」とのことです。
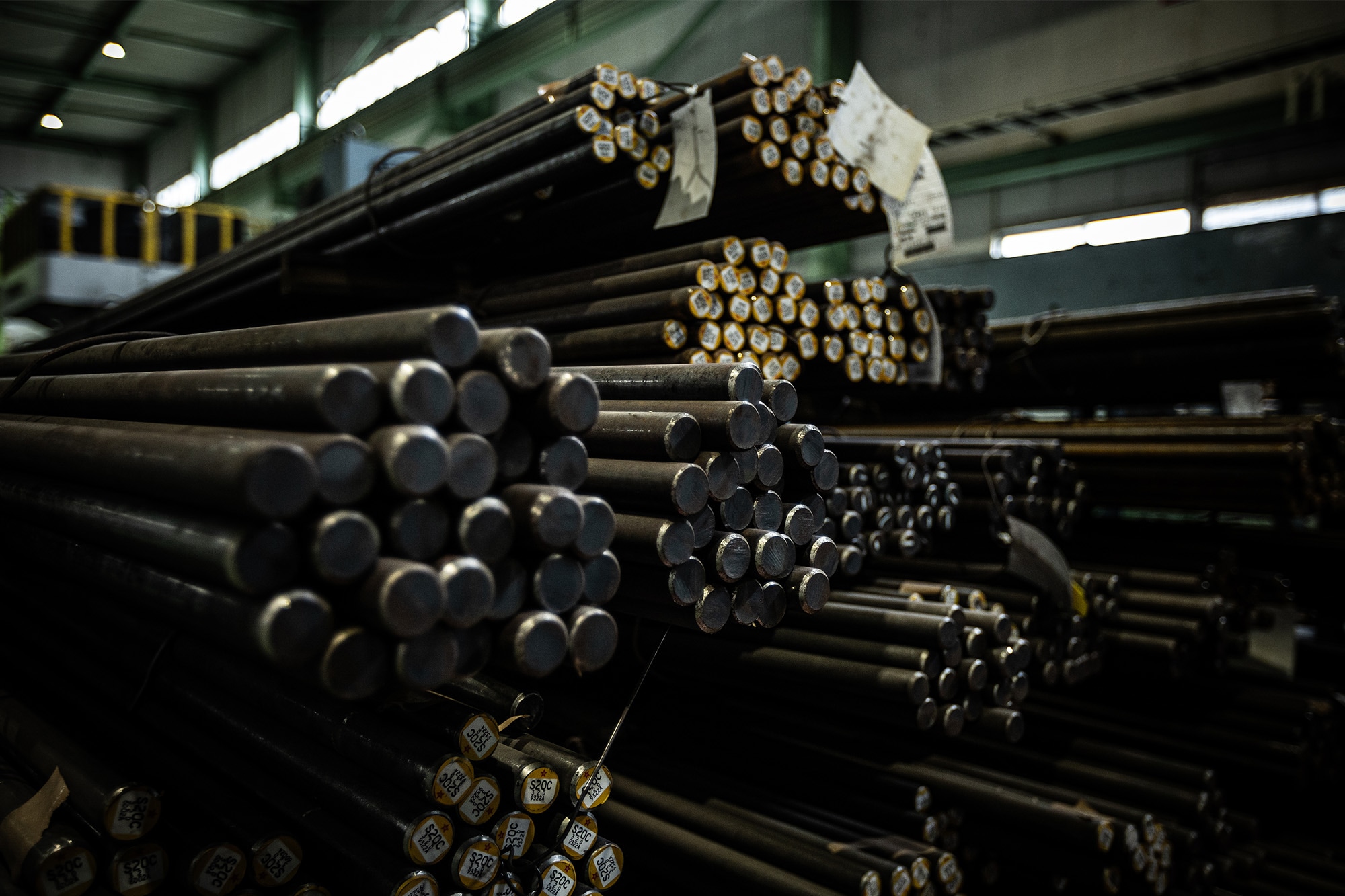
「いいものをつくるには、やっぱりいい素材が大切です。日本製のほうが、圧倒的に純度が高いんですよ。鉄には基本的にニッケルとかクロムとか、いろいろな物質が入っているのですが、その量が違うんですね。これが、アイアンの打感の良さや仕上がりにも関わってきますし、たとえば航空機や新幹線の部品、医療関係の部品などにも、全部、日本製の鉄が使われているんですよ。純度の高さは、製鉄を行っている日本の各社のこだわりということでしょうね」
この軟鉄S20Cが、機械で次々と切断されていきます。もちろん、機械から出てくるものは、「X PROTOTYPEアイアン」のヘッドに合わせた長さになっており、余分な部分が出ないようにミリ単位で調整されています。このいわゆる丸棒は、少し離れた場所にある加熱炉に運ばれて、鍛造の工程の前に1000度以上まで熱せられます。加熱炉は、実際に火を出すわけではなく、電子レンジのような仕組みで丸棒を熱くしていくのだそうです。
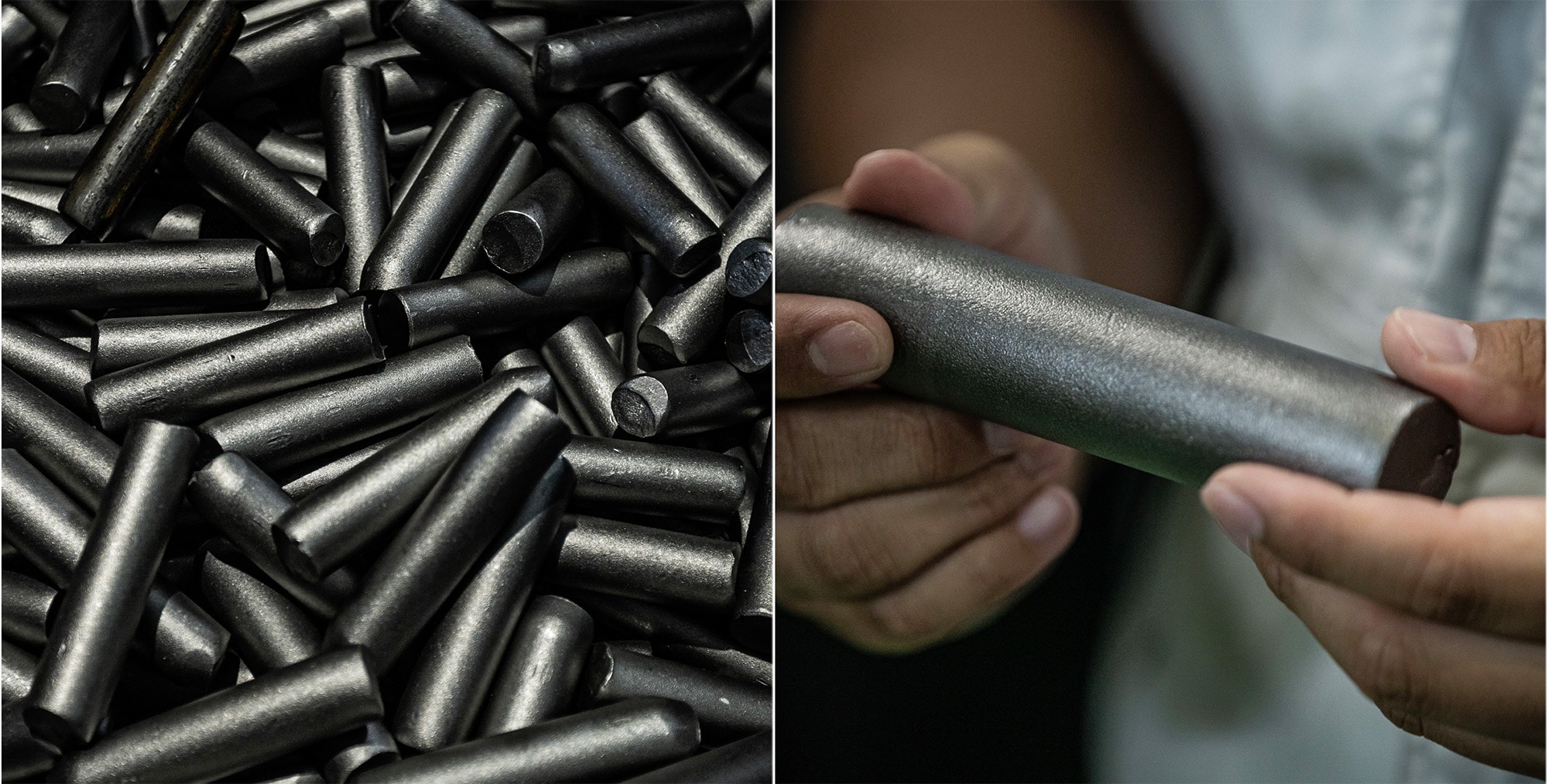
熱せられた丸棒は、いよいよ「X PROTOTYPEアイアン」のユニークな製法の1つである鍛造の工程に入ります。株式会社ササキの鍛造機は、写真のように非常に巨大です。一般的な鍛造機は2トンほどの力で叩くものとなっていますが、この鍛造機はチタンも成形できるほどの力があり、その数値はなんと最大で約1600トン(「X PROTOTYPEアイアン」は600トンで鍛造)! あまりに力が強すぎるため、この鍛造機は工場の床に置かれてはおらず、地面にしっかりとした基礎をつくり、さらに防振装置なども入れ込んで設置しているのだそうです。
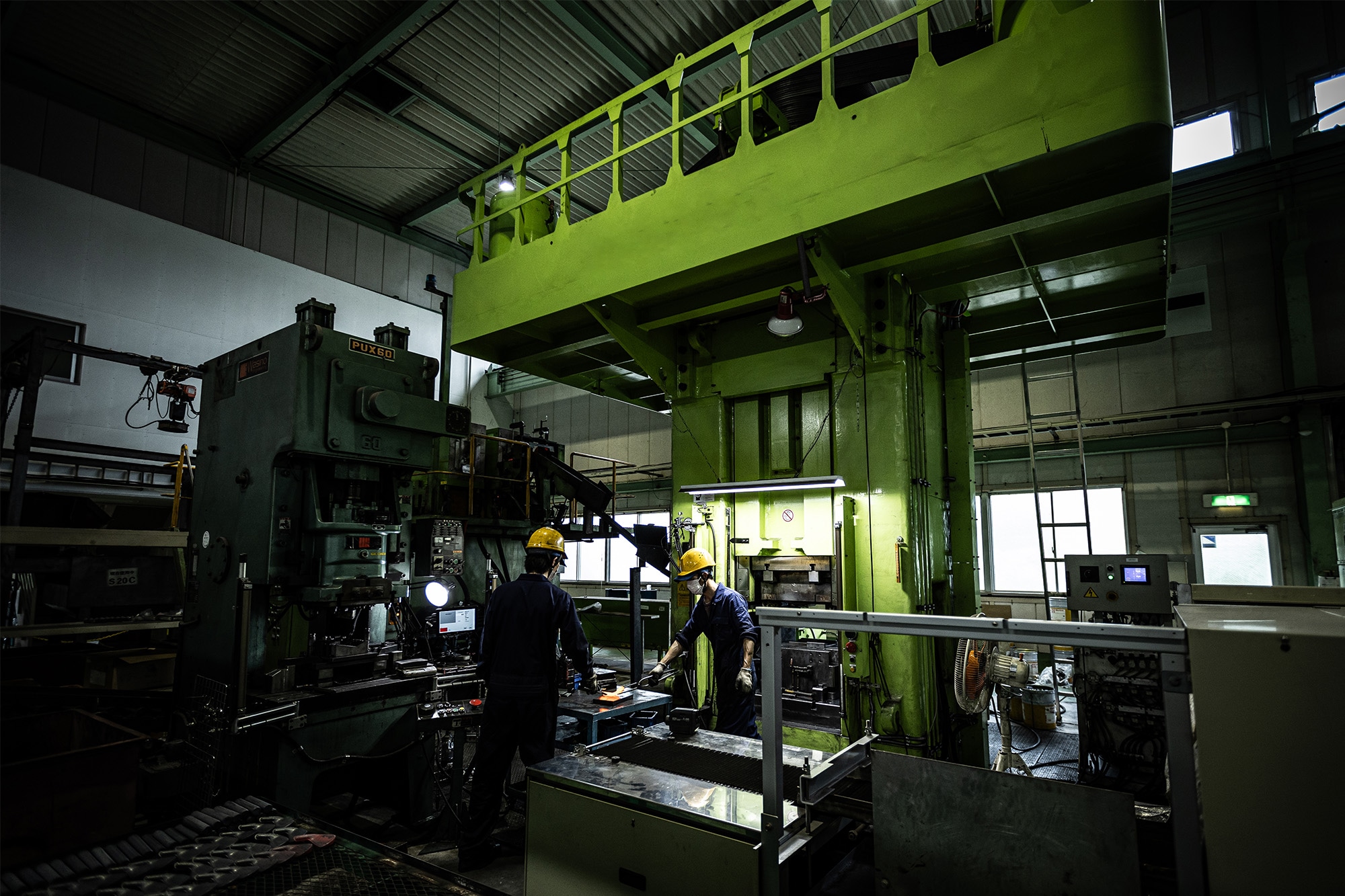
「X PROTOTYPEアイアン」を鍛造する際の金型は専用のものではなく、株式会社ササキが所有しているもののうちの1つで、鍛造された軟鉄が、「X PROTOTYPEアイアン」のヘッドよりもかなり大きめのサイズとなって出てきます。これを、後ほど見ていく機械加工で削り出していくことになります。通常、軟鉄鍛造アイアンは、複数の金型を使って数回叩くことにより成形されていきますが、何度も熱したり叩いたりするほど硬くなり、その分、打感が損なわれていきます。一方、鍛造が1回の場合、表面は比較的硬くなりますが、内部には柔らさが残っているため、硬い周囲の部分を削り出して形づくっていく「X PROTOTYPEアイアン」の打感は非常にソフトなものとなります。また、コストがかかる金型をつくらなくて済んでいるため、「X PROTOTYPEアイアン」のような小ロット生産も可能となっています。

鍛造は番手ごとに行われ、4番を300個叩いたら、次に5番を300個というふうに鍛造していきます。金型をセットする準備に、2~3時間かかってしまうからだそうです。また、丸棒だけでなく金型も熱せられます。たとえば冬場に、金型が冷たく、素材は温かいという状態となると、叩いたときに素材が割れてしまうからで、そのときの気温を考慮しながら金型の温度も調整されます。

余裕のあるサイズに鍛造されたヘッドは、他にあまり類がない、もう一つの工程である削り出しのため、鍛造機とは別の棟に向かいます。削り出しは、CNCという機械加工機で行われます。コンピュータで制御されており、決められた速度や移動量で刃物を当て、自動的に削り出していくものです。「X PROTOTYPEアイアン」では、余分な鍛造部分を大まかに加工する粗加工、フェース面とホーゼル内外径加工、スコアライン加工、キャビティ加工というふうに工程を分けて、複数のCNCで削り出していきます。ヘッドごとに全部の工程を通しで行うことももちろん可能ですが、それでは1日あたりの加工数が減ってしまうので、流れ作業のような形式が採用されています。「X PROTOTYPEアイアン」における加工時間は、フェース面とホーゼル内外径加工のものは5時間以上(一度に4つのヘッド)、キャビティ加工に至っては11時間(一度に12個のヘッド)もかけているとのことです。
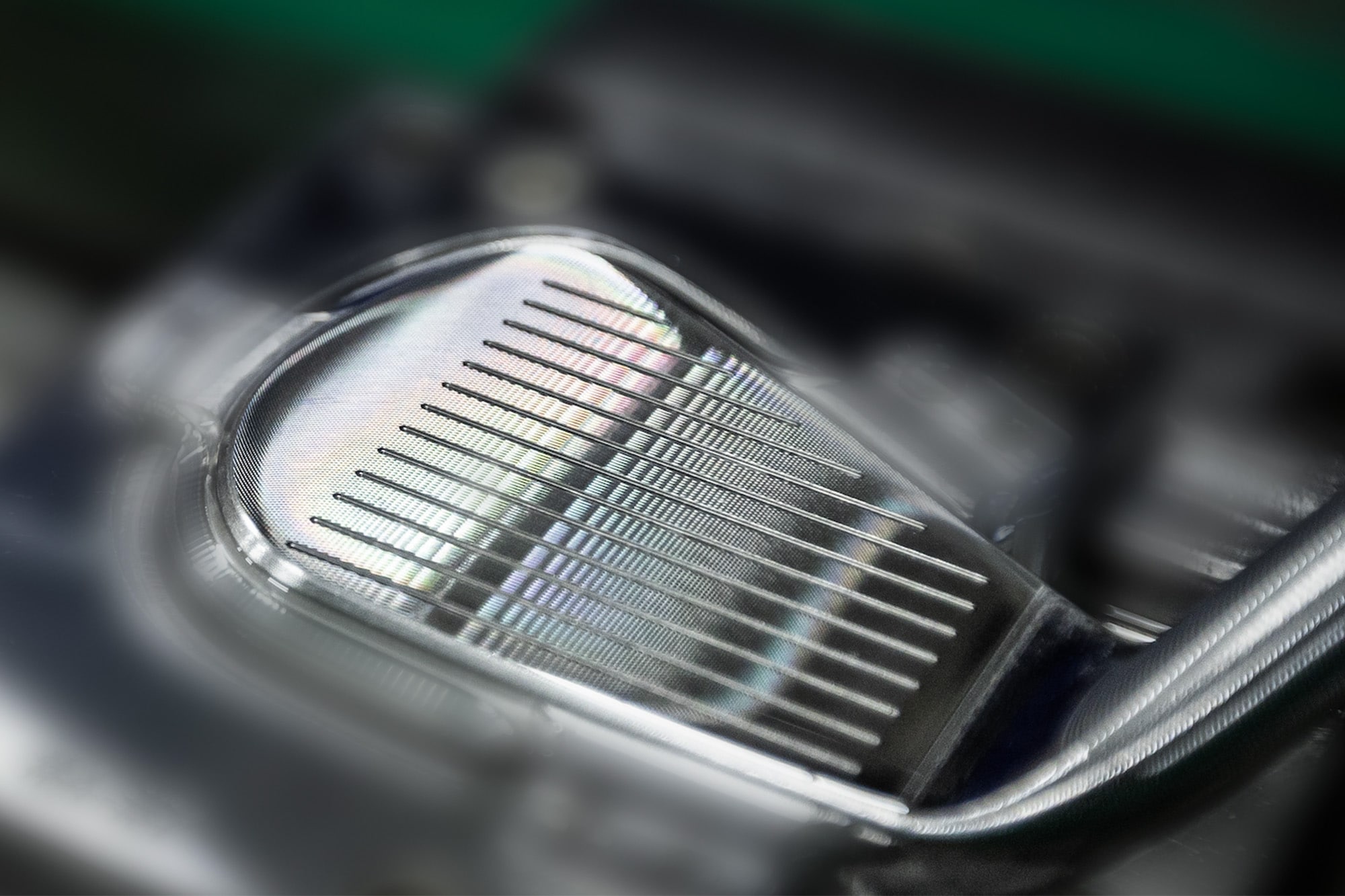
CNCの隣では、キャロウェイとX PROTOTYPEのロゴ、番手の彫刻が行われています。こちらもコンピュータで設定されて自動で削り出されていきます。番手によってヘッドの形状が異なることで彫刻する刃物が当たる角度も変わってしまうため、4~7番と8~PWで分けて作業を行っているそうです。
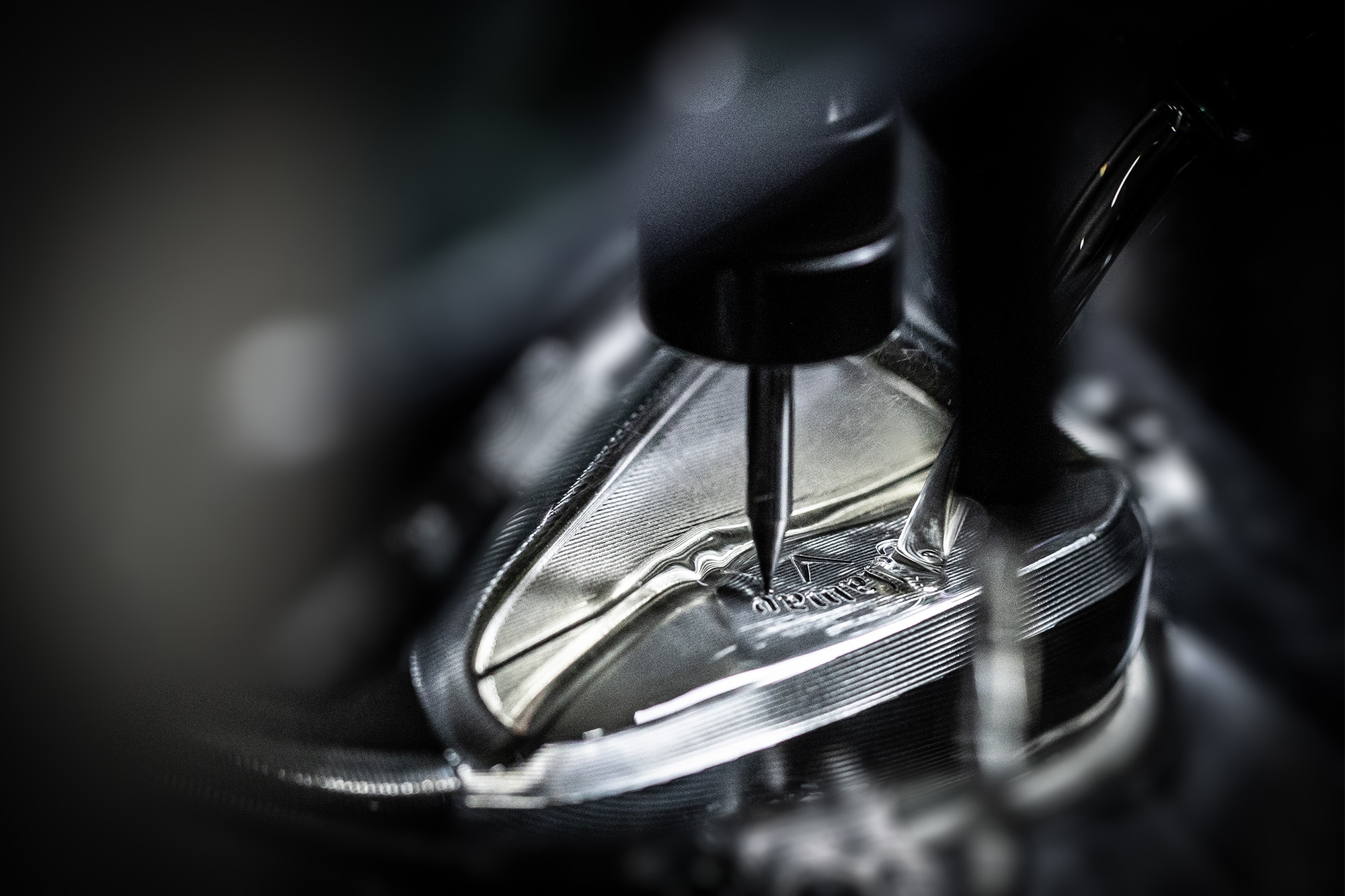
削り出しが終わったヘッドは、研磨の作業でさらに仕上げられていきます。削り出しの際にできた加工の跡を除去したり、角が立った部分を自然な形に丸めたり、キャロウェイのロゴがあるバックフェース下部を鏡面加工したりする作業です。ただし、「X PROTOTYPEアイアン」は、時間をかけて通常よりも細かく丁寧に削り出されているため、火花が出るほどに研磨する必要はないそうです。株式会社ササキの佐々木恭太郎専務によると、「本当に皮を剥く程度のイメージで、ほぼ、磨くという感覚です」とのこと。ちなみに、株式会社ササキの祖業は研磨であり、佐々木政浩社長(下写真)の研磨技術は社内でも群を抜いているそうです。
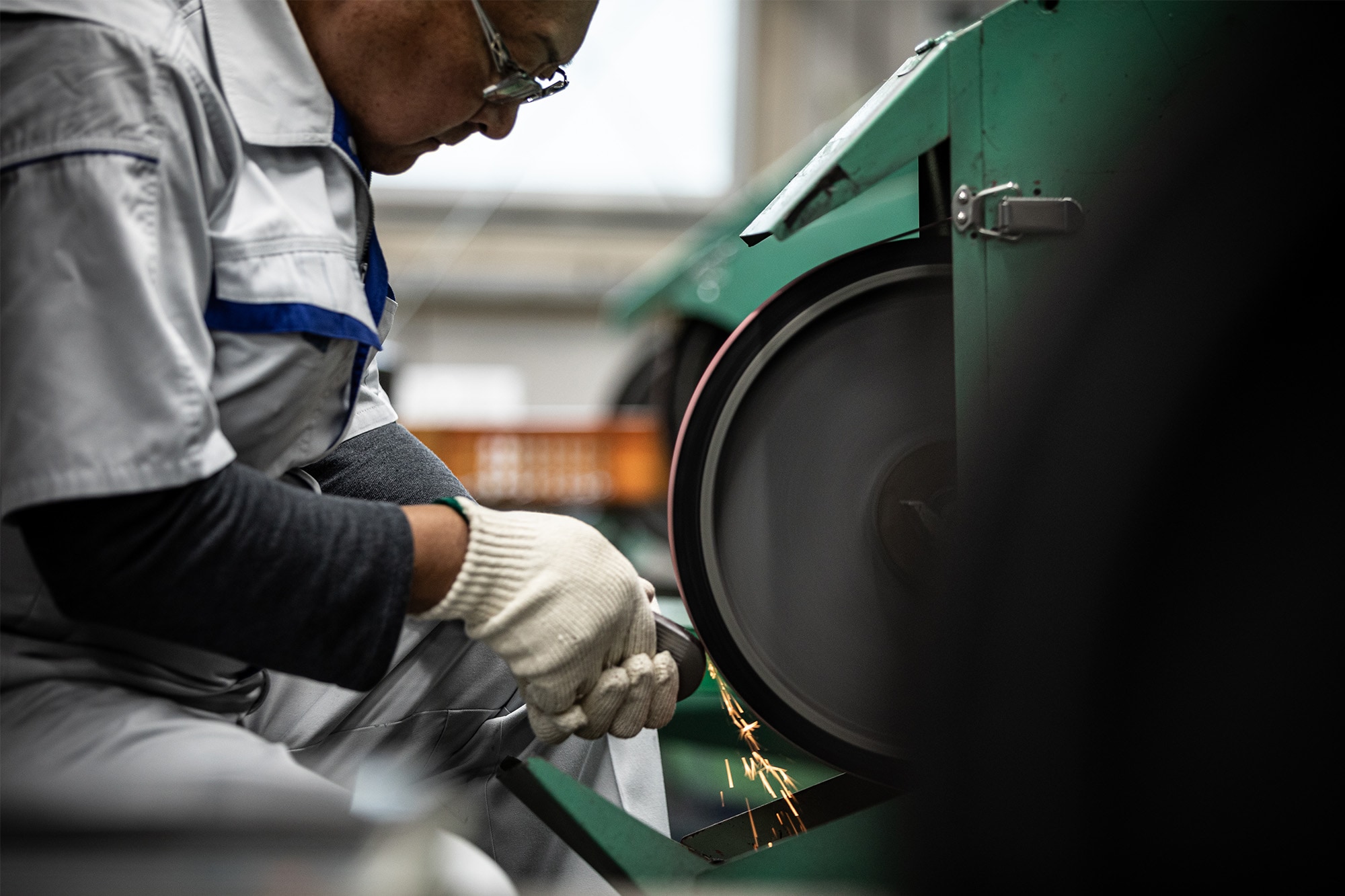
研磨まで終わったヘッドは、ロフト角やライ角といった数値が設計どおりにできているかどうかを厳密に検査したのち、メッキ処理されます。メッキは他企業に外注され、1週間から10日くらいで戻ってきます。もちろん、メッキ後のヘッドも同様に、さまざまな数値が細かくチェックされます。
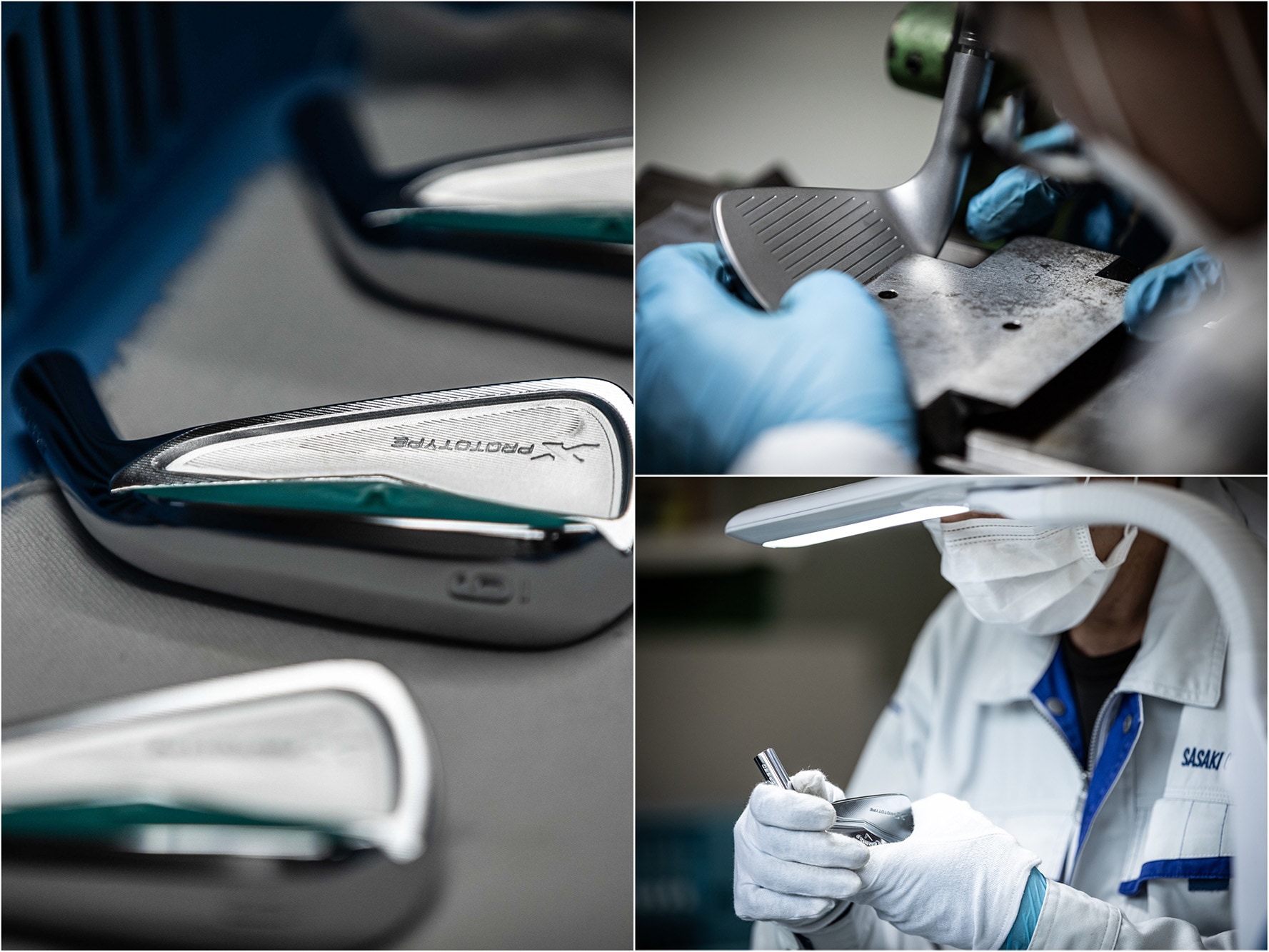
「X PROTOTYPEアイアン」も、いよいよ最後の仕上げです。この段階では、フェース面のブラスト処理のためのマスキングと、ブラスト処理が終わったヘッドのロゴ、番手表示への色入れ、シリアルナンバーの彫刻、そしてシュリンクの作業が行われます。もちろん、マスキングや色入れはすべて手作業です。なかでもマスキングは、かなり重要な作業とのこと。ブラストしたところとしていないところの境目のラインが曲がって見えたりすると、ゴルファーによっては構えたときにフェースが真っすぐターゲットを向いていないように見えたりすることもあるためです。
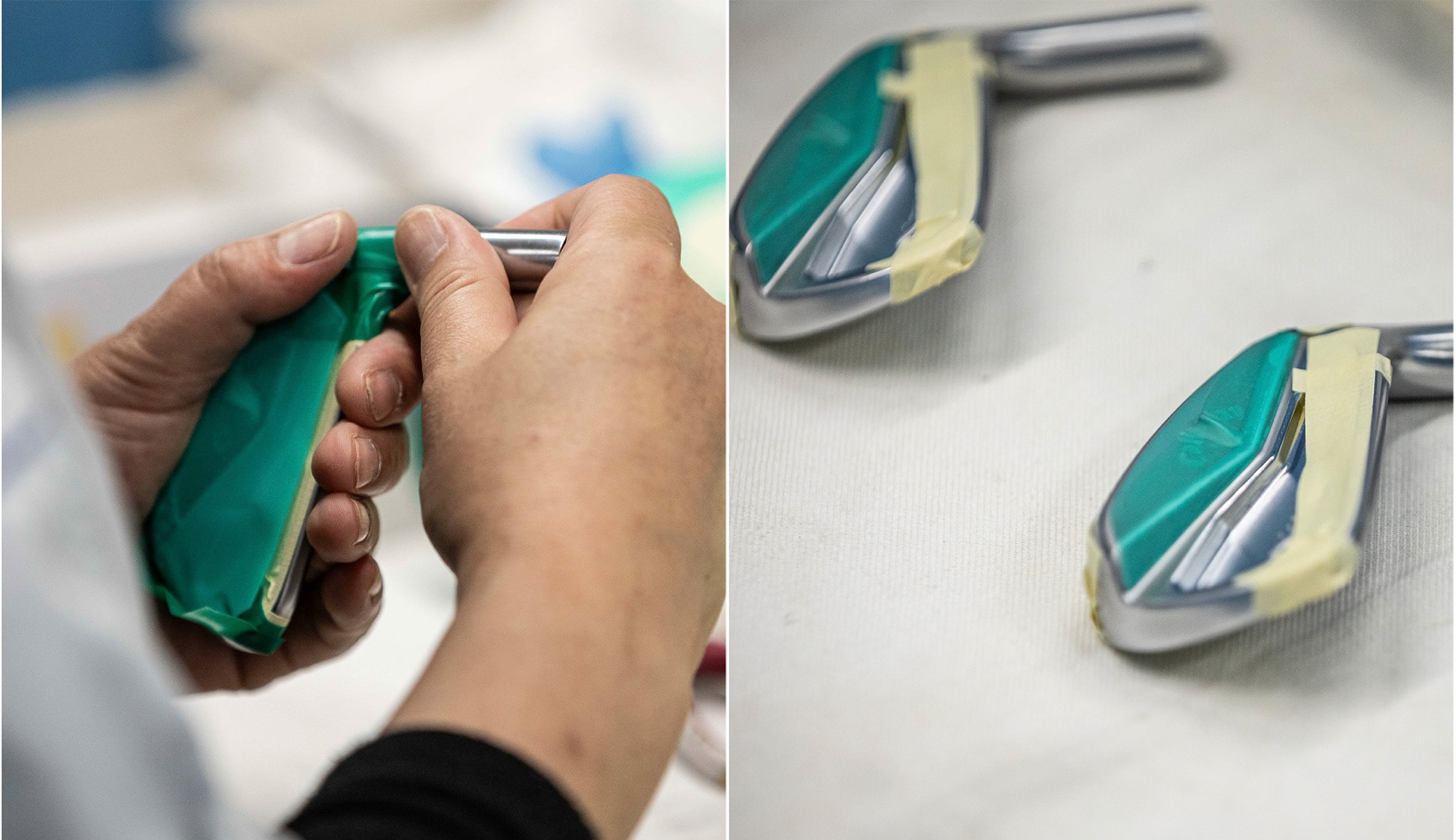
マスキングされたヘッドは、隣の作業スペースにある機械でブラスト処理が行われます。ブラスト処理は、スピン量などにも関係しますが、主な目的は光の反射を抑え、構えたときに眩しくないようにすることにあります。自動で処理することも可能ですが、「X PROTOTYPEアイアン」では、すべて手作業となっています。手作業のほうが、きれいに仕上がるそうです。
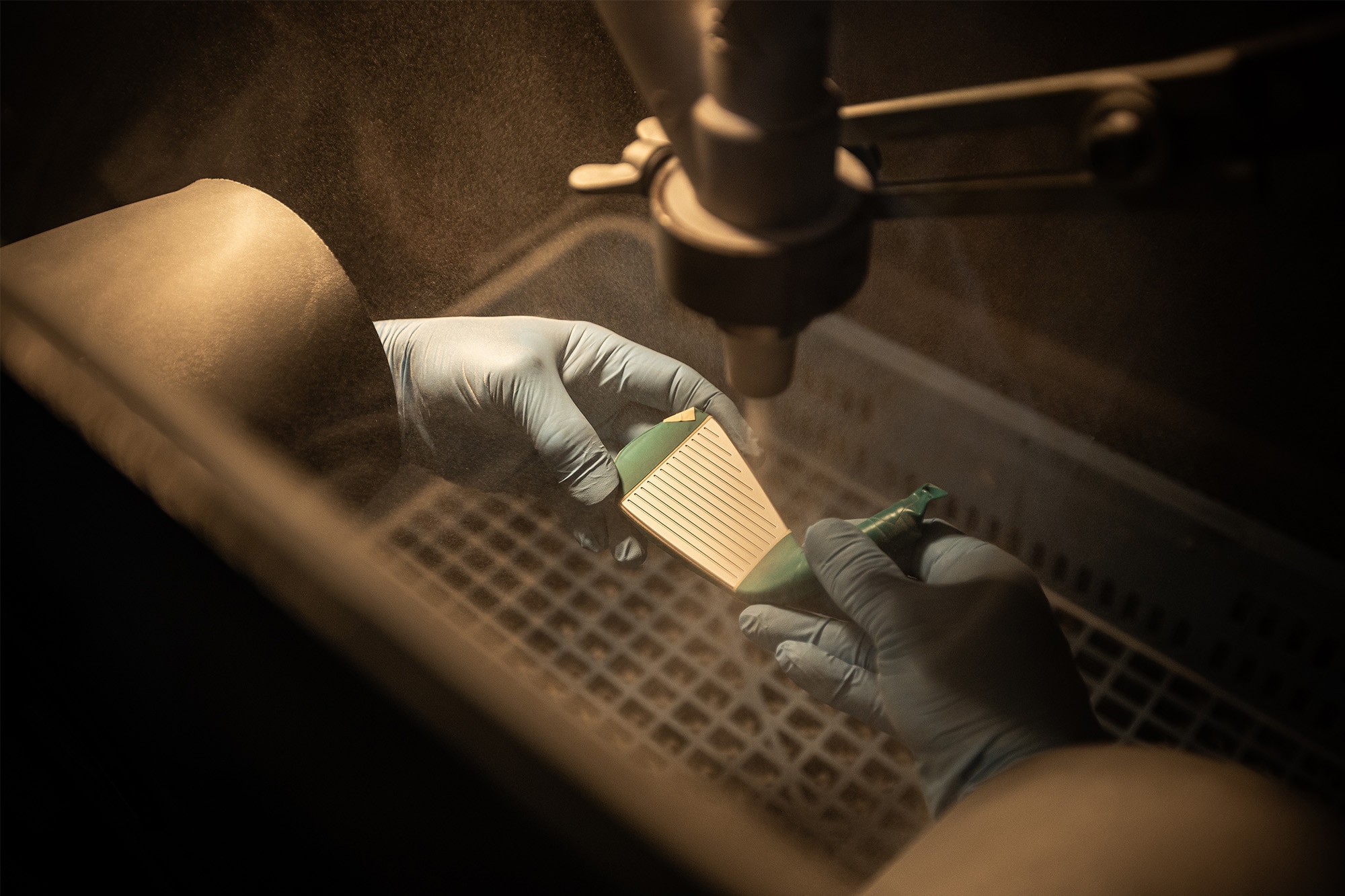
サンドブラストは、砂などの研磨剤を噴出するサンドブラスターという箱のなかにヘッドを入れて行われます。2種類の研磨剤を使用して、2段階で仕上げていくそうです。サンドブラスト処理を行うスタッフの方にお聞きすると、メッキが剝がれてしまわないようにコントロールしながらやらなければいけないため、メッキの塗膜の厚みなども把握しているとのこと。それができるようになるには、やはり経験が重要で、長くこの作業をやっていると、研磨剤を当てたときなどの感触で、「これ以上やったらまずい」「これ以上、圧を上げるとダメ」といった感覚が研ぎ澄まされていくそうです。サンドブラストの処理が終わると、元の作業スペースに戻ってシュリンクがかけられ、ついに出荷ということになります。
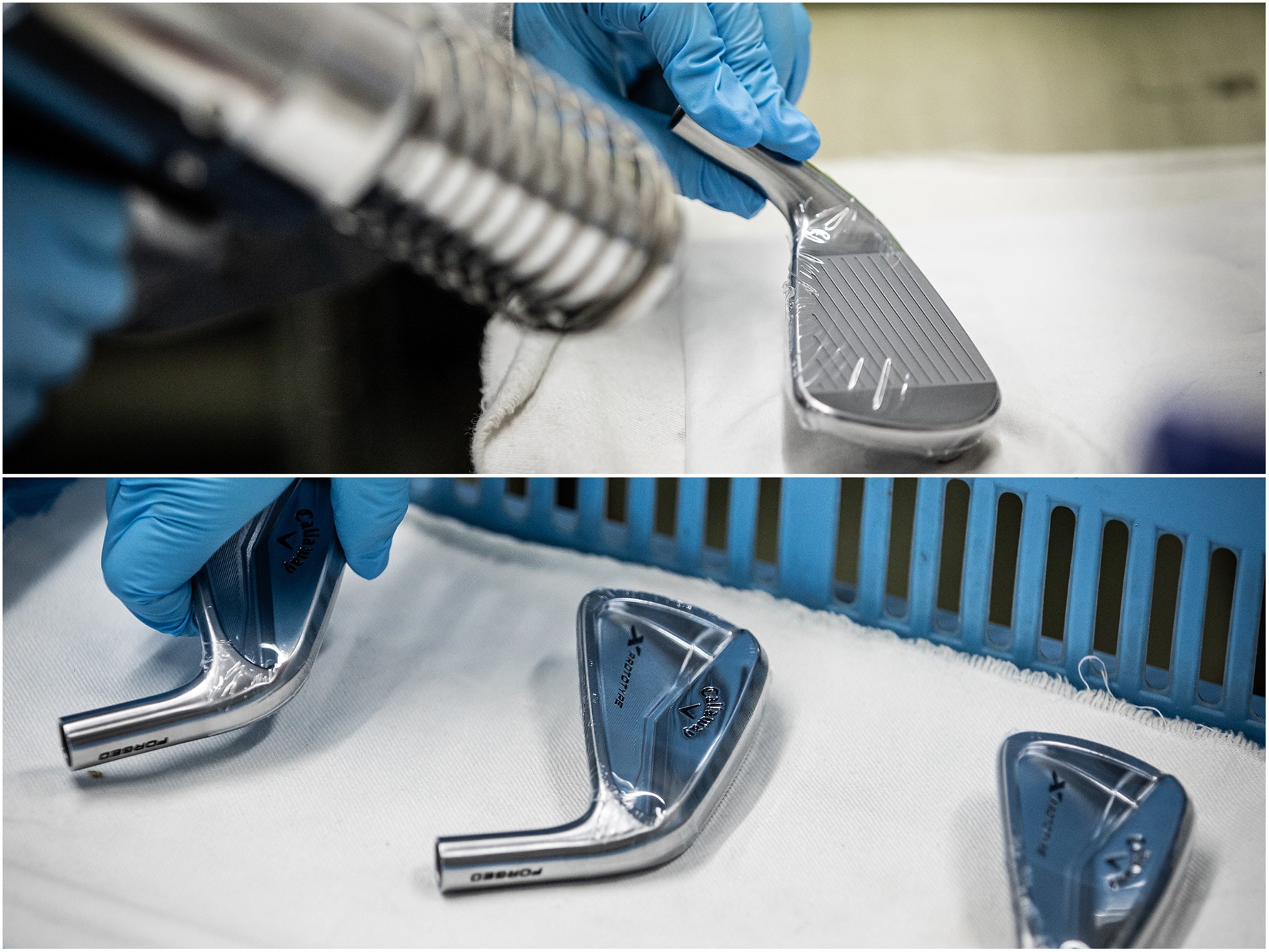
最後に、佐々木恭太郎専務に、「X PROTOTYPEアイアン」がいかにスペシャルなモデルなのかを、ヘッド製作の観点から語ってもらいました。返ってきた答えは、先にも触れましたが、「研磨量が少ないところです」というものでした。
「それはつまり、形状のズレがないということです。削り出しの機械加工で限りなく完成に近いものにまで追い込んでいるので、研磨量も少なくなるんです。また、研磨で人の手が入ると、それも形状のズレにつながってきますから、極力、研磨はしないようにして、異例とも言える少なさにしています」
「機械加工で追い込んでいる」というのは、丁寧に多くの時間をかけていることを意味しています。
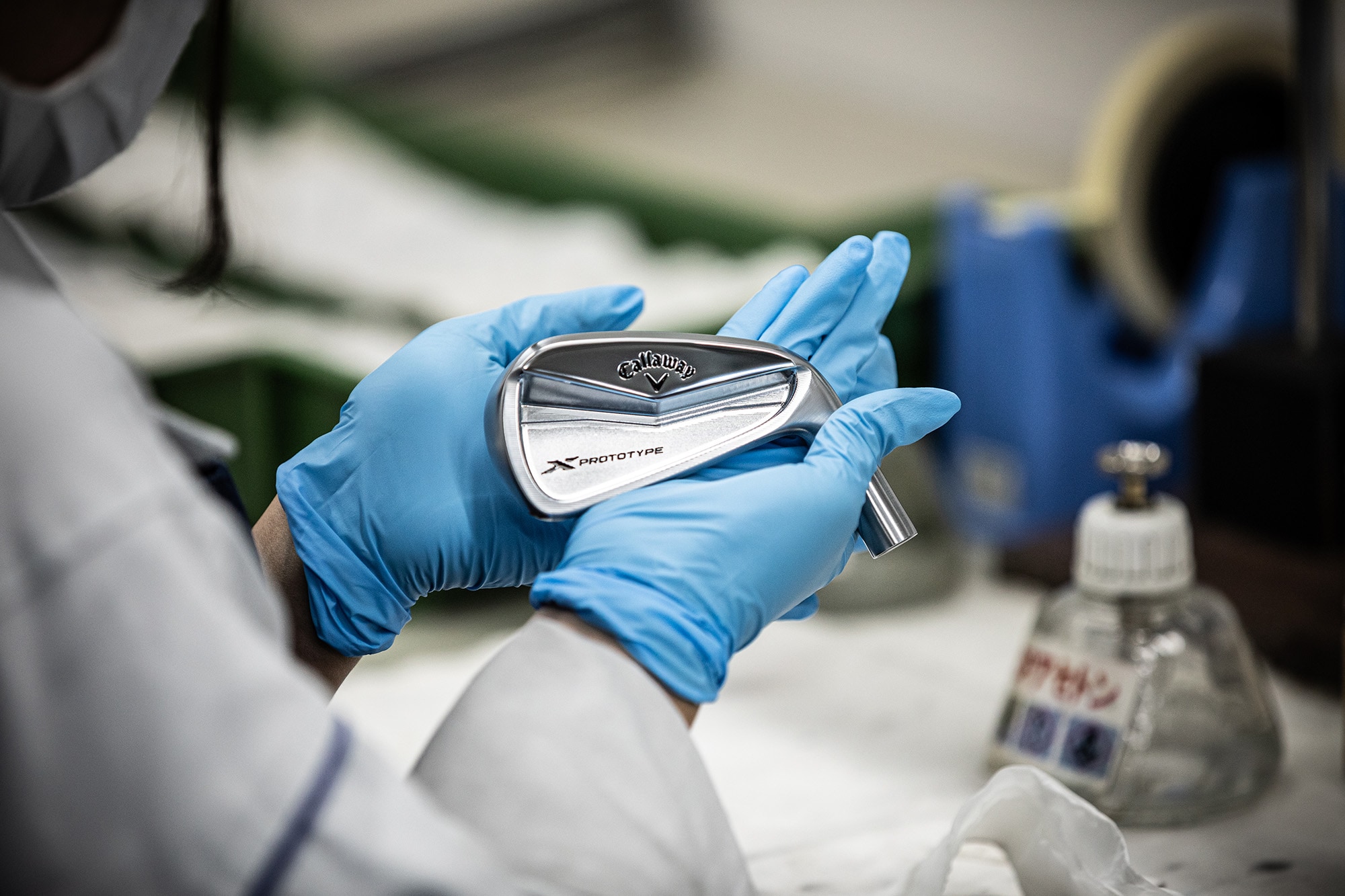
「機械加工で刃物が通ると、ヘッドの表面には1本の筋が入って目が残るんですけど、その目が極力細かく薄くなるよう、プログラムを組んでいます。目が濃い、深いと、時間はかかりませんし、早くやる方法はいくらでもあります。でも、その目を取るのが大変です。一方で、目が薄いと研磨は少なくて済みますが、そうするには機械加工に時間をかけて削らなければいけません。もちろん、使う刃物も重要で、1本10万円ほどするものですが、定期的に交換し、使い古したものを使わず、なるべく新品のもので削るということも、目の薄さに繋がってきます。スコアラインの彫刻に関しては、キャロウェイさん専用の刃物も使っています。そのあたりは間違いなく、今回のアイアンと他の製品の違うところじゃないでしょうか」

鍛造1回による打感の良さと、削り出しによる精巧で美しい仕上がりが特徴的な「X PROTOTYPEアイアン」は、8月8日より受注開始となります。すべてカスタムでの取り扱いです。詳細は、キャロウェイ オンラインストアでチェックしてみてください。
X PROTOTYPEアイアンの製品ページはこちら